Nowadays, more and more steel mills use Pure Ca cored wire and Seamless Pure Ca cored wire to feed into ladle. However, some of them do not know approaches for feeding cored wire into ladle, precautions during feeding process and reasons for low calcium recovery. We will introduce and analyze this below and advise you at last part of this article.
Content
Reasons that we feed calcium cored wire into ladle
The most widely use is feeding calcium cored wire into ladle
Using aluminium metal to make deoxidize process. It can reduce oxygen content in molten steel. After producing high-melting-point compound —— Al2O3, can make them gather, come-up, eliminate by blowing argon gas, stirring or other approaches. But this approach has a drawback that it is difficult to eliminate clearly at some time because of small volume of Al2O3, it affects stability of pouring and cleanliness of molten steel. Thus, calcium process method is came up.
Calcium process is an approach that deoxidize, desulphurize and clean molten steel. Calcium can change high-melting-point Al2O3, MgO and Al2O3 inclusions into low-melting-point liquid inclusions that makes impurities mix easily, enlarge volume and then you can blow argon gas to make them come-up and eliminate. Therefore, calcium process is used widely. There are many methods to add calcium such as direct addition method, catapult addition method, injection addition method and feeding wire method. But you have to pay attention that the method to get the highest calcium recovery is feeding wire method among these methods. And there are many factors involved in this method are controllable. Thus, it is the most common method that feeding CaSi cored wire into ladle to clean molten steel at present.
Introduction of calcium cored wire
Calcium cored wire includes CaSi(Calcium Silicon) cored wire, CaFe(Ferro Calcium) cored wire and Pure Calcium cored wire.
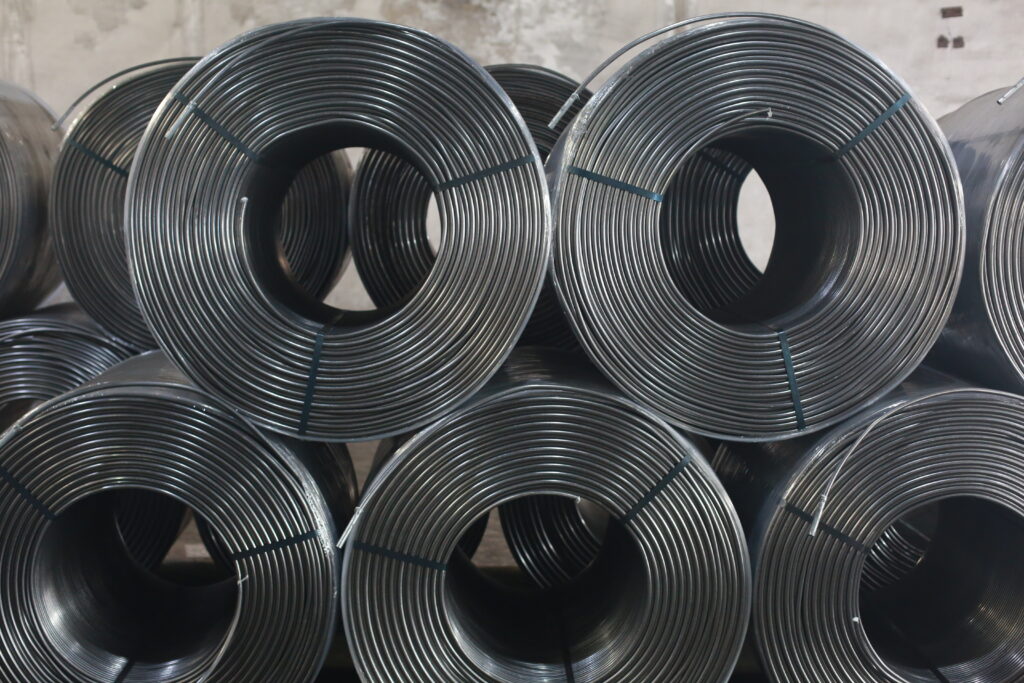
Fig.1 Calcium cored wires
CaSi cored wire: using 0.4 mm+/-0.05 mm steel strip covered 0-2 mm calcium silicon powder to make cored wire. Common diameter is 9/13 mm. It has the highest cost performance, utilized the most widely. Many steel mills mainly use CaSi cored wire.
CaFe cored wire: the outer is also 0.4 mm+/-0.05 mm steel strip, core powder is mixture that calcium and proportional ferro powder. It can finely adjust elements to improve recovery of metal, rare earth and other elements to ensure stability for elements.
Pure Calcium cored wire: using 0.6 mm+/-0.05 mm steel strip covered pure calcium to make cored wire. Common diameter is 9 mm. Calcium recovery is the most stable, at the same time, the costs also higher. But it can process refined steel grades suitable for CaSi cored wire and CaFe cored wire. Calcium recovery improved to 52% above. It attracts a majority of steel mills in North America and Europe market. And over half of steel mills have been used calcium cored wire.
Otherwise, Seamless Pure Calcium cored wire is also a kind of calcium cored wire. Its structure is same to pure calcium cored wire, only outer steel strip do not have any gaps. It can be fed in deeper ladle and reduce spillage of molten steel, sometimes, even avoid. At the same time, it can increase use efficiency of cored wire significantly, calcium recovery can be improved 2-5 times.
Effects of feeding calcium wire into ladle
1. Decreasing sulphur content in molten steel, reducing sulphide inclusions, it is difficult to transform during rolling process;
2. Oxide inclusions in molten steel are changed into uniformly dispersed calcium oxide inclusions. It reduces size of inclusion and improves cleanliness of molten steel;
3. It is easy for changing high-melting-point Al2O3 inclusions into low-melting-point calcium aluminate inclusions to add calcium in Al killed steel. It is convenient to gather and come-up. And preventing nozzle from clogging.
What will be used while feeding calcium cored wire into ladle?
Cored Wire, Feeding Machine, Ladle, Molten Steel, Stabilizer, Auxiliary Equipment, etc. Different approaches will use different equipments. Thus, what kinds of equipments will be used, it depends on situations to determine.
Precautions
1. Feeding Cored Wire Angle: feeding machine should be fixed above ladle in one side, between calcium cored wire and gear wheel of feeding machine is arc shape, it is convenient for calcium cored wire to flow rapidly during feeding process. Feeding wire gun is perpendicular to solution in the ladle, it is convenient for calcium cored wire to be injected in deep position of molten steel directly.
2. Feeding Cored Wire Speed: feeding calcium cored wire speed is controlled 120-160 m/min ordinarily. Different steel grades, volumes of molten steel have different best feeding cored wire speeds, it depends on actual situation to choose.
3. Feeding Cored Wire Quantity: unless it depends on steel grade, component, performance to choose proper quantity, it maybe has negative effect on quality of molten steel.
4. Feeding Cored Wire Position: it also has significant effect on calcium recovery. The feeding position of solid pure calcium cored wire should be chosen in the center of molten steel downward-flow and tried to keep away from argon blowing bright circle.
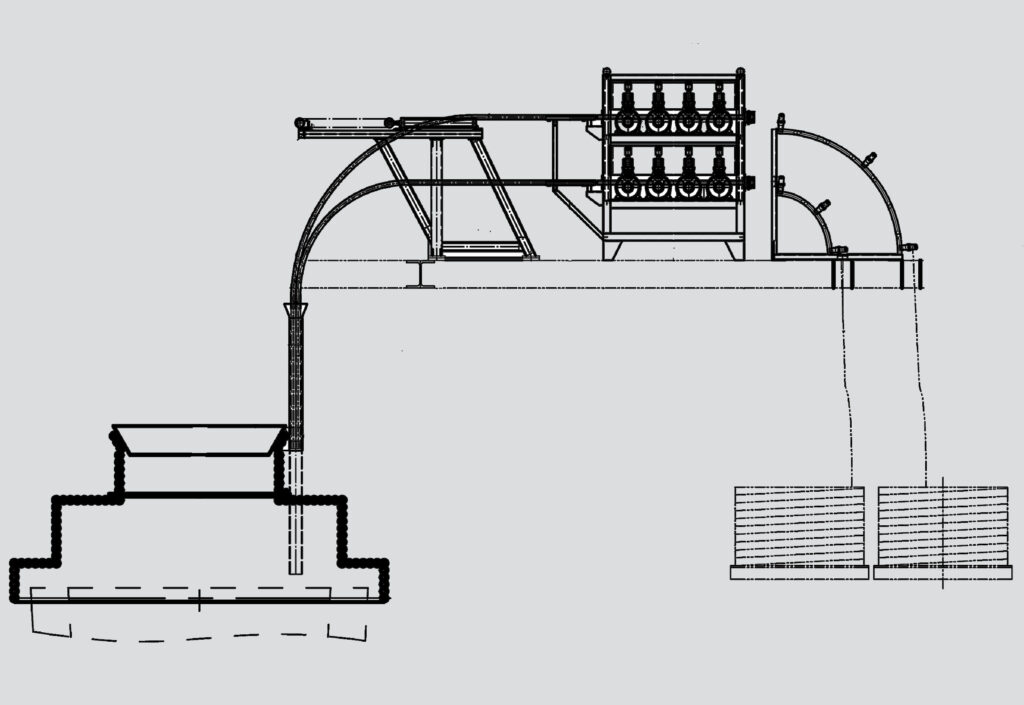
Fig.2 Sketch map for feeding cored wire into ladle using feeding machine
Possible results after feeding
Feeding Cored Wire Speed: it is the key factor to decide that whether get anticipated results or not during feeding cored wire process. If speed is so fast, on one hand, molten steel is boiled drastically because produced a lot of calcium vapour in some regions. On the other hand, calcium vapour doesn’t have enough time to dissolve adequately and most of them come-up, it reduces calcium recovery. On the contrary, slow speed causes that calcium cored wire cannot be fed deep into molten steel, it come-up to molten steel surface before dissolved in molten steel completely, the quantity of calcium ion doesn’t reach the lowest quantity to process inclusions in molten steel, it also leads to low calcium recovery.
Molten Steel Process Temperature —— it relates to calcium recovery directly. The higher molten steel’s temperature in ladle, the higher vapour pressure of calcium, the faster calcium escape speed from molten steel, the shorter interaction time between calcium and molten steel, the lower effective rate and recovery for calcium process.
The longer effective working time to feeding machine under best speed circumstance, the higher effective rate and recovery for calcium process. If feeding machine stops feeding cored wire, you must start using spare feeding cored wire system. And if you don’t have spare feeding cored wire system, you should make ladle stop working immediately.
If cored wire is broken during feeding process, you should stop feeding until cored wire is fixed to machine again.
Additionally, feeding cored wire incidence angle is also essential for calcium recovery. Whatever feeding cored wire incidence angle is rather large or rather small, calcium cored wire reacts above molten steel and isn’t able to make deslagging process on the bottom of molten steel. It affects efficiency of feeding cored wire and effect for removing impurities of refined steel.
How to use? What’s kind of cored wire purchased can avoid some problems?
Advice:
Adding calcium in molten steel as more as possible, reducing burning loss, extending calcium staying time in molten steel. These approaches can improve calcium process efficiency furthest and reduce steel producing costs.
Calcium content of solid pure calcium cored wire is higher than CaFe cored wire. If feeding cored wire speed is same, molten steel is boiled more drastically and it is profitless for calcium absorption.
At the same time, solid pure calcium cored wire compared with CaFe cored wire, it has some advantages such as uniform diameter, excellent tensile strength, great toughness, wire broken hardly, etc. It is beneficial to control quantity of feeding cored wire precisely.
Besides above advice, we also utmostly recommend you to purchase seamless cored wire JINLI GROUP produced.
Seamless Cored Wire JINLI GROUP produced has several advantages as follows:
1. Increases 30% of calcium recovery than Normal Cored Wire.
2. Effectively reduce spillage of liquid steel. And significantly improve the utilization of the ladle.
3. The Seamless Cored Wire can be used in the ordinary feeding machine to feeding line and suitable for all kinds of the steel grade.
4. Due to the product technology advantage,reduce oxidation process,increase the storage time of calcium.
In conclusion, various cored wires have their own advantages and disadvantages, user in steel mill should decide to choose suitable cored wires by their requirements. But in economic benefit and calcium recovery, it is a developing trend that CaSi cored wire, CaFe cored wire and other alloy cored wires are replaced by Seamless Pure Calcium cored wire and Pure Calcium cored wire gradually.
If you have any questions or needs, please contact us without any hesitation. We will revert as soon as possible.
2 回复
评论被关闭。