Introduction:
In the family of casting alloys, the development of various casting alloys depends on the development of their advantages and the suppression of their disadvantages. Compared with cast steel and non-ferrous alloys, cast iron has better casting performance. Therefore, the utilization rate of molten iron is high and the product is widely applicable.
In the competition of materials, improving the strength of cast iron, increasing toughness, and eliminating internal defects are very important for reducing the weight of castings, extending service life, and saving materials. In order to ensure the reliability and stability of cast iron performance, good molten iron quality is first required. Therefore, pre-furnace treatment must be done well!
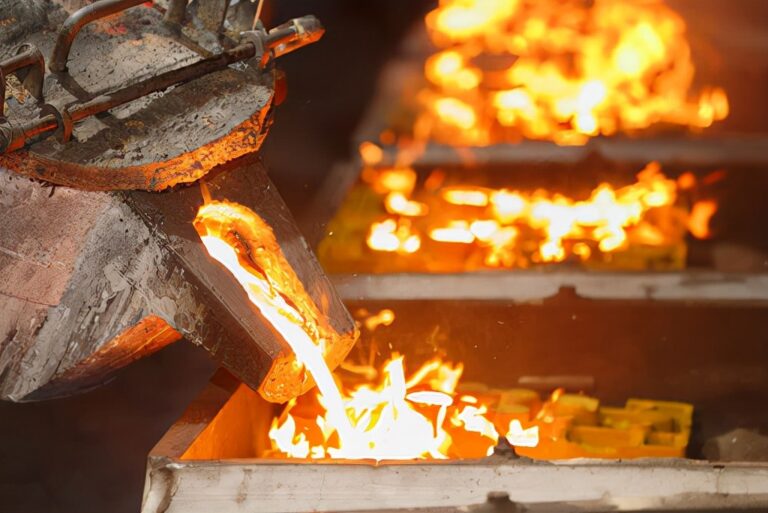
1. Desulfurization
Desulfurization of molten iron can reduce the amount of spheroidizer and the number of sulfide slag inclusions in castings. In developed countries, ductile iron production almost all adopts desulfurization technology, requiring S≤0.01% after desulfurization. Under my country’s conditions, the target position is S≤0.02%, and Xichai and Changchai can reach S≤0.015%.
The bottom of the ladle Na2CO3 flushing method is simple but the desulfurization rate is low and the effect is unstable. During the treatment, smoke and dust pollute the environment and irritate the throat. In the ductile iron workshop with large-scale production, it is advisable to place the desulfurizer on the liquid surface and use mechanical stirring, shaking bag method or pneumatic stirring method for desulfurization. Among them, the pneumatic method is relatively simple, consumes less power, and is the most popular. The pneumatic desulfurization device can be installed upstream of the fore furnace for continuous desulfurization, or intermittent desulfurization can be performed in a single bag in front of the furnace. The pneumatic source is mostly N2.
Desulfurizers are divided into two categories: CaC2 series and CaO. CaC2 has a good desulfurization effect and can reduce sulfur from 0.04~0.06% to below 0.01%. The slag is granular and easy to remove, but it is expensive and has a high melting point. It is also hindered by transportation and storage, so it is limited to nearby supply. CaO series is more commonly used. No matter which series of desulfurizers, they should have moisture-resistant and explosion-proof characteristics. The composite desulfurizer made of active CaO after surface film treatment and additives is not affected by moisture and has high desulfurization efficiency. The desulfurization rate of pneumatic desulfurization is 60~90%. For factories with small output, low melting point composite desulfurizers should be used for single bag flushing desulfurization, with a desulfurization rate of 30-50%. At this time, the desulfurized slag is molten.
After pneumatic desulfurization, the molten iron enters the induction furnace to raise the temperature.
2. Deslagging
The deslagging process can be carried out in the bag or in the induction furnace. Sprinkle the deslagging agent (slag-aggregating agent) on the liquid surface to form a molten layer immediately, which plays a covering and slag-aggregating role. The deslagging agent expands when heated, and many small holes are produced in the molten layer, which plays a good insulation role.
Deslagging agents are divided into three grades: low, medium and high. The products made from the raw ore after simple crushing and screening belong to the low grade, and are produced in all provinces. It is no longer favored by foundries. The mid-range deslagging agent has some selection of the raw ore, and adds water washing and other processes, which can meet the basic requirements of castings and are accepted by most factories. Imported high-grade deslagging agents select high-quality ore sources, and the processing procedures are different from the general ones. This product spreads quickly on the liquid surface, covering the entire liquid surface. It has excellent slag removal ability, low dosage, does not stick to the furnace lining and ladle, and can be lifted up as a whole with a stick. The slag removal is convenient and thorough. In the past three years, it has begun to receive attention from the domestic industry.
3. Spheroidization
Spheroidization treatment is still mainly based on the ladle flushing method. The selection of spheroidizing agent depends on the furnace, iron tapping temperature, desulfurization and ductile iron type. Generally speaking, Mg7~9%, RE3~7% spheroidizing agent is used for cupola iron liquid, low Mg (5~6%), low RE (1.5~2.5%) spheroidizing agent is used for induction furnace iron liquid, and some factories still use Mg8RE3 spheroidizing agent. JB/T9228-1999 standard stipulates that the composition range deviation of Mg and RE is ±1%, and some factory standards have been reduced to ±0.5%, and there are also clear regulations for Ca, Al, etc. In the quality of spheroidizer, attention should be paid to the MgO content, the degree of segregation of components and the concentration of particle size. Any spheroidizer with uneven particle size, much powder and dark color should not be used.
In principle, as long as the chemical composition of molten iron and the inoculation process are mastered, the above-mentioned spheroidizer can be used to produce cast ductile iron. However, some factories also use spheroidizers for cast ductile iron. Generally, Ba and Bi are contained in cast ferrite spheroidizers, and Ba and Sb are contained in cast pearlite spheroidizers. However, for important crankshaft castings above QT700-2, it is not recommended to use Sb-containing spheroidizers. At this time, the matrix should be controlled by adjusting the content of Cu, Mo, etc. It must be pointed out that regardless of whether cast spheroidizers are used, inoculation is always an important link that cannot be ignored.
Heavy rare earth magnesium-containing spheroidizers are used for thick-walled ductile iron parts. In order to prevent spheroidization decline and graphite distortion, the amount of Si should be reduced, and the process of increasing the number of graphite balls and refining the diameter of graphite balls should be adopted.
The ladle treatment method greatly reduces the smoke and light pollution during treatment. It is a simple process that saves spheroidizing agent and ensures the quality of spheroidization, and is worthy of promotion. Inspired by the steel liquid wire feeding technology, wire feeding spheroidization has been successfully used in enterprises such as Xinxing Casting Pipe Company after experiments. Wire feeding spheroidization is a process in which the wire feeder continuously feeds the alloy cored wire to the bottom of the ladle for spheroidization treatment. This process can accurately control the amount of residual magnesium and has the characteristics of one high and three lows, namely high spheroidization quality, less slag, less temperature drop, and less pollution. The outer skin of the cored wire is 0.3mm thick cold-rolled steel skin. The core material generally contains 25~30% Mg and has a composite component of Ca, Ba, (RE), etc. The cost of the wire feeding method is 20~40% lower than that of the flushing method, which is very attractive to mass-produced cast pipe plants, automobile foundries, etc. At present, many domestic units can supply wire feeders and cored wires as a complete set. The cored wires are divided into multiple varieties such as spheroidization, creeping, inoculation, desulfurization, carbon addition and alloying.
In-mold spheroidization is to set up a reaction chamber in the pouring channel, and the molten iron will undergo spheroidization reaction while flowing. In-mold spheroidization has good working conditions, less oxidation loss, and a Mg absorption rate of up to 80%, which overcomes the spheroidization decline and inoculation decline and improves the performance of ductile iron. In-mold spheroidization has strict requirements on the sulfur content of molten iron, and the process yield rate of castings is low. It was used in China in the 1970s, but is no longer seen in production.
4. Inoculation
Inoculation is an important link in improving the quality of cast iron. After more than ten years of efforts, my country’s inoculants have basically achieved serialization and commercialization. At present, domestic inoculants are mainly silicon-based and carbon-silicon-based.
Silicon-based inoculants have a low melting point and are suitable for various molten irons with high carbon and low carbon, high sulfur and low sulfur, and are the most widely used. Special ferrosilicon has a strong inoculation effect, a small amount of use, and causes little fluctuation in the chemical composition of molten iron, and the quality of cast iron is stable. FeSi-Ba-Ca is the first choice for the widest coverage. It significantly increases the number of eutectic clusters, inhibits the formation of D and E type graphite in gray iron and promotes the formation of A type graphite, improves the spheroidization level, and has good anti-decay properties when Ba, especially Ba and Ca, coexist. FeSi-Sr is an inoculant suitable for thin-walled engine parts. It has excellent anti-chill ability without significantly increasing the number of eutectic clusters, so it can eradicate the problem of leakage caused by shrinkage. In the production of ductile iron, the inoculation effect of Sr is weakened due to the presence of Ce. Zr-containing ferrosilicon has a similar effect to Ba-containing ferrosilicon, but it is weaker. However, Zr has a degassing function and a micro-alloying effect, which stabilizes the mechanical properties of cast iron. Zr-containing ferrosilicon has a high melting point, so Zr-Mn often coexists to lower its melting point. High-Ca inoculants, such as CaSi, have the functions of desulfurization, deoxidation, anti-chilling and increasing graphite nuclei. They were widely used in the 1950s and 1960s. Later, due to the improvement of coke and molten iron quality, CaSi was rarely used alone, and was occasionally used in combination with FeSi or FeSiRE. The carbon (graphite) in the carbon-silicon inoculant makes this inoculant have excellent anti-chilling ability. It is more suitable for gray iron parts with many corners and thin walls produced by high-temperature molten iron. It can also be used as an option for hydraulic thin-walled parts with anti-leakage requirements. Carbon-silicon inoculants should not be used in ductile iron production.
The replacement of large-dose inoculation in the tapping trough by various forms of post-inoculation is a major trend in the development of inoculation methods. Post-inoculation should pay attention to the particle size and particle size uniformity of the inoculant, especially in ladle flow inoculation and pouring flow jet inoculation. If the particle size is too large and poor absorption will produce defects such as hard spots and intergranular inclusions in the casting. When using high-efficiency inoculants, avoid excessive inoculation to prevent shrinkage, pores and graphite segregation.
There are many methods for in-mold inoculation. At present, most of them are to place block inoculants at the bottom of the sprue for over-flow inoculation. This method grasps the nucleation peak of inoculation and can theoretically achieve the best inoculation effect.
5. Alloying
Common alloying elements of cast iron include Si, Mn, Cu, Cr, Mo, Ni, Sn, Sb, V, Ti, P, etc. Among them, Si, Mn, Cr, Mo, and P are added in the form of ferroalloys, Cu, Ni, Sb, and Sn are added in the form of metals, and V and Ti are added in the form of ferroalloys or VTi pig iron. The timing of adding is after the furnace (cupola), in the furnace (induction furnace), or in front of the furnace, depending on their melting point, oxidizability, and density. In order to facilitate the melting and absorption of high-melting-point ferroalloys, in addition to controlling the particle size, the use of heating alloying agents or wire feeding methods is a more ideal measure.
Practice shows that adding a portion of FeMn and FeCr together with silicon-based inoculants has a weighted effect on inoculation. Where possible, delaying the addition of low-alloying elements is beneficial to the performance.