Content
Definition
Generalized ferroalloy is a kind of product that as a deoxidizer, element additive added into liquid steel during steelmaking to make steel possess some property or reach some requirements. Intermediate alloy that combined Fe and one or some elements mainly used in steelmaking. In steel industry, all of intermediate alloy during steelmaking usually was called ferroalloy whether contains Fe or not (e.g. CaSi alloy). Customarily, it also include some pure metal additives and oxide additives. It should be noted that all of steel belong to ferroalloy, it makes ferroalloy become most widely used alloy.
Uses
Basic Classification
There are many types and classifications of ferroalloys in the globe. Classifying according to below approaches usually:
1. Main elements:
Mainly have ferroalloys series of Si, Mn, Cr, V, Ti, W, Mo, etc.
2. Carbon contents:
Have high carbon, medium carbon, low carbon, micro carbon, ultra-micro carbon, etc.
3. Two or more alloy elements:
Main types are AlSi alloy, CaSi alloy, AlMnSi alloy, CaSiAl alloy, CaSiBa alloy, etc.
4. Production methods:
Have blast furnace ferroalloy, electric arc furnace ferroalloy, perrin process ferroalloy, vacuum solid reduction ferroalloy, electrolysis ferroalloy. Additionally, also have oxide block ferroalloy, exothermic ferroalloy and other special ferroalloy.
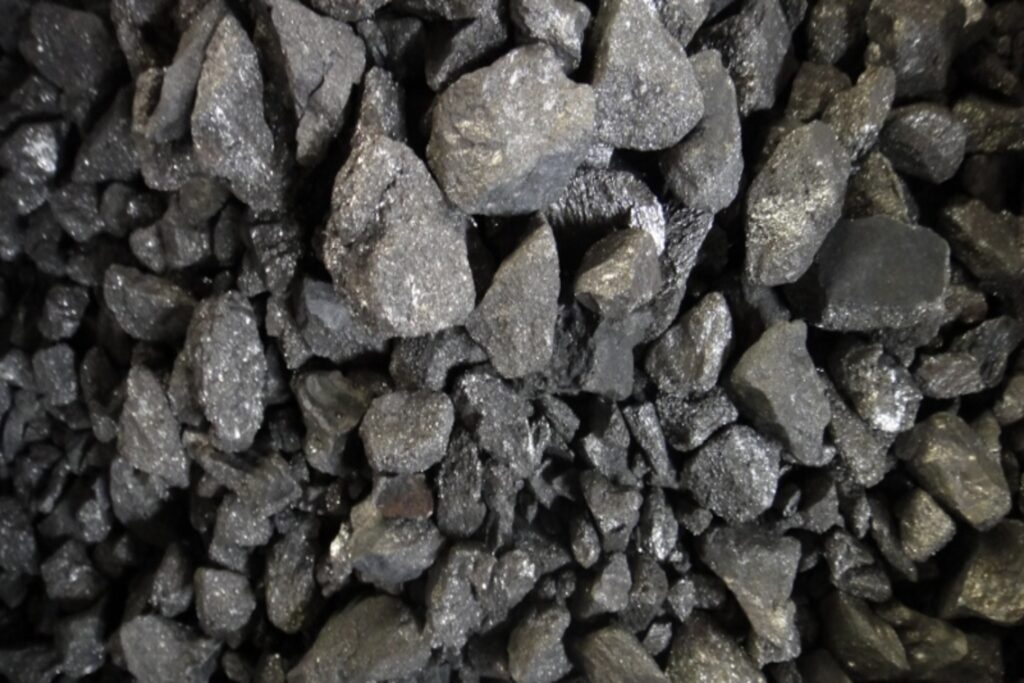
Fig. 1 Ferro boron alloy
Common Uses
1. Deoxidizer:
Main use of ferroalloy is deoxidizer. Including, SiMn, FeMn and FeSi are used most widely. Strong deoxidizer are: Al(FeAl), CaSi, SiZr, etc.
Blowing oxygen to make molten steel decarburize and eliminate phosphorus, sulphur and other harmful impurities during steelmaking. This process will increase oxygen content in molten steel. However, the higher oxygen content, the lower mechanics property for steel. As a consequence of this property, adding some elements that combining capacity with oxygen stronger than ferro and its oxide eliminated from molten steel as furnace slag easily, this procedure can eliminate oxygen in molten steel.
2. Alloy additives:
Common types used as alloy additives are: FeMn, FeCr, FeSi, FeW, FeMo, FeV, FeTi, FeNi, FeNb(Ta), rare earth ferroalloy, FeB, FeP and so on.
Silicon can improve elasticity and magnetic conductive for steel prominently, thus, silicon series ferroalloy can be used in many smelting processes such as structural steel, tool steel, spring steel and silicon steel. Generally speaking, silicon content in steel is about 0.15% – 0.35%, in structural steel is 0.4% – 1.75%, in tool steel is 0.3% – 1.8%, in spring steel is 0.4% – 2.8%. While, in silicon steel, can reach 2% – 3% approximately.
Manganese can reduce brittleness of steel, consummate heat-producing function, improve steel strength, hardness and wear resistance. In steelmaking field, over 90% manganese was utilized. To some degree, it is a basic and functional raw material that inevitable in producing high-quality steel.
3. Inoculant:
Changing solidified condition is one of methods to improve castablity for steel. In order to changing solidified condition, we add some ferroalloy before pouring as crystal nucleus and makes formed graphite fined and distracted, so that improve casting property.
4. Reductant:
Producing other ferroalloys and nonferrous metals by metallothermic reduction method. It can be used as alloy additives of nonferrous alloy and some used in chemistry industry and other industry.
Silicon alloy used in producing FeMo, FeV and other ferroalloys as reductant. In addition, SiCr and MnSi alloy as reductant used in producing medium carbon and low carbon FeMn respectively.
Additionally, many ferroalloys are stipulated several levels according to smelting requirements, alloy element or carbon content. And restricts impurity content seriously.
Complex ferroalloy, a kind of ferroally, contains two types or more alloy elements. When you use this kind of ferroalloy, can add deoxidizing or alloying elements. It is beneficial to smelt steel process. And it can comprehensively utilize symbiotic ore resources economically and reasonably. Common types are: SiMn, CaSi, SiZr, AlSiMn, CaSiMn, rare earth FeSi, etc.
Pure metal additives smelting steel used are: Al, Ti, Ni, metal Si, metal Mn, metal Cr and so on. Some oxides that easy to reduce also used to replace ferroalloys such as MoO, NiO. Besides, FeN alloy, FeCr processed by nitriding, FeMn, exothermic ferroalloy included exothermic agent, etc. These can also instead of ferroalloys.
Smelting
Property
Main element of ferroalloy possesses high melting point usually or its oxide is difficult to reduce. Thus, it is difficult to smelt pure metal. If it combined with ferro, it will be easy to reduce. During steelmaking process using ferroalloy, ferro not only unharmful but also beneficial because it is easy to melt in molten steel. Therefore, deoxidizing and adding alloy in smelting steel producing process, most of them are ferroalloys. However, ferroalloy is so brittle that does not use as metal material.
Smelting Development
Starting smelting low-grade ferroalloy using crucible in 1860 approximately. Then, progressed smelting FeMn and FeSi (contains Si below 12%) in blast furnace gradually.
From 1890 to 1910, many mills start using electric arc furnace to produce ferroalloy in France. H.Moissan has made systemic tests to element that is difficult to reduce using electric arc furnace. At the same time, French metallurgist P.L.T. applied in industrial produce. At that moment, all of mills used coke and charcoal as reductant to reduce relevant ores. And most of products are high-carbon.
After 1920, in order to meet premium steel and stainless steel development requirements, started entering into a new stage that producing low-carbon ferroalloy. On one hand, developed many approaches that smelting some carbon-free ferroalloy and pure metal by thermite process on basis of using thermite process to smelt metal technique in 1898 came up by K.Goldschmidt. On the other hand, desilication refining process that oxidize silicon ferroalloy in electric arc furnace has been developed. Because of high producing expense by thermite process, desilication refining process was applied more widely. So far, most of high-carbon, medium-carbon, micro-carbon FeCr (ferrochromium), medium-carbon and low-carbon FeMn (ferromanganese) and metal Mn has been refined by this process. Perrin Process is accelerated by hot mixing with ore(liquid), lime(melt) and SiCr alloy.
This is a further development for desilication refining process. Otherwise, mills also used electrolysis process to produce alloy additive (e.g. metal Mn) and produced ultra-micro carbon FeCr (contains carbon extremely low) by vacuum decarburization process. Many years later, it has been progressed to refine FeCr and FeMn using pure oxygen blowing process.
Main Methods
1. Blast furnace method:
Producing low-grade ferroalloy mainly. Producing FeMn procedure is similar to raw steel smelting by blast furnace.
Advantages:
Consecutive produce, high producing efficiency, low costs;
Disadvantages:
Low temperature in furnace, difficult to reduce some elements, limited types produced.
2. Electric furnace method:
It is main method to produce ferroalloy, production surpass using other producing method. Main equipment is electric furnace, it divided into two parts: reducing electric furnace(ore-smelting electric arc furnace) and electric arc furnace(refining furnace). Products include: FeSi, industrial silicon, high carbon FeMn, CaSi alloy, high carbon FeCr and so on.
Reducing electric furnace method:
Electrode is inserted in furnace burden, makes submerged arc operation, utilizing resistance, electric arc to heat ore and reduce it. Thus, it is also called ore-smelting electric arc furnace.
Electric arc furnace method:
It is a flexible technique to smelt ore and metal utilizing high temperature produced by electric arc. It is effective to eliminate sulphur, phosphorus and other impurities. Furnace temperature is controlled easily. It is proper to smelting premium alloy steel because of small floor area.
3. Outside furnace method:
It is a kind of smelting method using heating energy produced by reducing reaction. Tube smelting furnace is main equipment used in this process.
In addition, also have other methods to smelt, we don’t introduce in detail here.
Environmental Pollution
Main contaminants during ferroalloy producing process are smoke, waste slag, waste water. Among these contaminants, smoke is the most hazardous to environment. To some extent, it affects environment severely. According to regulation, exhaust gas can be divided into contain particulate matter(PM) exhaust gas and contain gaseous contaminants exhaust gas.
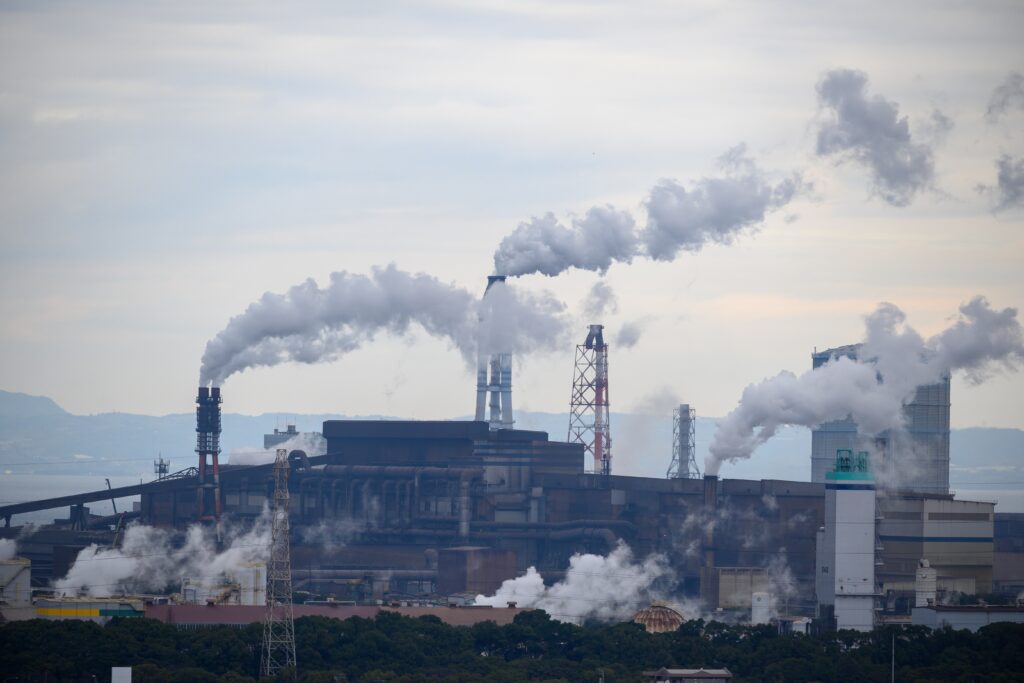
Fig. 2 Factory emits a lot of exhaust gases to the environment
In ferroalloy plant, exhaust gas is caused by ore-smelting electric arc furnace, refining electric arc furnace, calcining rotary kiln, multi-layer mechanical calcining furnace and so on. Another noticed factor is emission quantity. Many of ferroalloy plants emit a lot of exhaust gases with high concentration dust to environment. It is unfriendly behaviour to environment. 90% of exhaust is SiO2, remains are chlorine(Cl2), N oxide, carbon monoxide(CO), sulfur dioxide(SO2), etc. Otherwise, chromium(Cr) compounds polluted waste slag and waste water mainly.
Conclusion
As inevitable type to smelt steel, ferroalloy played a significant role in steelmaking. Its down stream is smelting. As a result of bulk power, we must focus on coal market situation. Frankly speaking, it links whole black production chain excellently as medium product. However, quartz stone is a raw material to produce industrial silicon and it combined black production chain and silicon industry each other. Therefore, ferroalloy is very important to link the preceding with the following.
If you have any questions or needs, please contact us without any hesitation. We will revert as soon as possible.