Many enterprises use the wire-feeding method for nodularization when producing ductile iron pipe fittings on vertical flaskless molding lines. However, sometimes the lower castings in the same mold turn out to be gray iron, while the upper ones remain ductile iron. What could be the reason? This article will answer all your questions.
Reasons for defect formation:
Challenges in Wire Injection Nodularization Process:
If the cored wire is not inserted deeply enough during wire feeding nodularization, the nodulizer may not fully diffuse or may float upward. The upper part of the iron melt can achieve nodularization, while the lower part may form gray iron due to insufficient nodulizer.
Insufficient wire feeding or improper timing may lead to inadequate residual nodularizing elements in the iron melt, making segregation more likely during pouring.
If the wire feeding amount is not precise, the feeding speed is unstable, or the position is suboptimal, the initial magnesium content in the treated iron melt may be too low, or its distribution may be uneven from the outset, exacerbating segregation issues in the mold cavity later.
After wire feeding nodularization, the magnesium in the iron melt decays over time (due to oxidation or vaporization). If the time from the nodularization station to pouring is too long, the initial magnesium content may drop excessively, making the lower sections more prone to magnesium deficiency and resulting in defects.
Potential Issues in the Inoculation Process:
Insufficient or uneven distribution of inoculant, insufficient inoculation in the lower part, small number of graphite nuclei, and difficulty in forming spherical graphite. Or the inoculant is concentrated in the upper part, promoting the formation of ductile iron structure, and the inoculation effect in the lower part is poor, resulting in the appearance of gray iron structure.
The inoculation effect is affected by the cooling rate. The lower molten iron cools quickly, and the inoculant may not fully function, with few graphite crystal cores, making it difficult to form spherical graphite. The upper molten iron has a good inoculation effect and good graphite spheroidization.
The inoculation effect is affected by the solidification rate. Rapid solidification of the lower casting may cause the inoculant to not have time to fully function, resulting in aggravated inoculation decline or even inoculation failure.
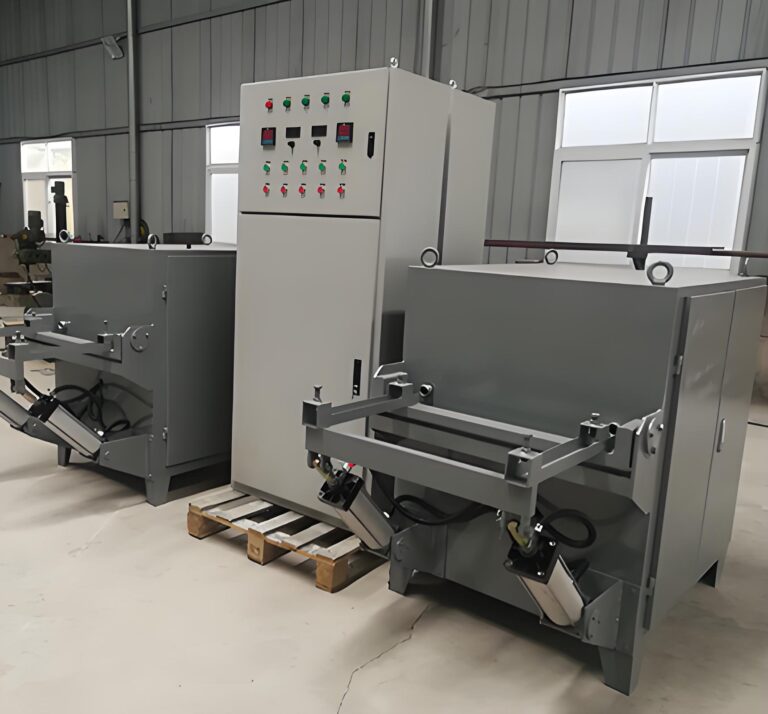
Possible problems in casting process:
During pouring, the molten iron flows from the gate through the cavity, and the lower molten iron is in contact with the air for a long time, resulting in a high degree of oxidation. The spheroidizing elements react with the inclusions generated by oxidation, reducing the effective content of the spheroidizing elements in the lower part, causing the lower structure to deviate from the characteristics of ductile iron and be closer to gray iron.
During pouring, the molten iron flows into the cavity from the upper part, and the temperature of the upper molten iron is relatively high, which is conducive to the full spheroidization reaction and the formation of ductile iron structure; while the temperature of the lower molten iron is low, the spheroidization reaction is not sufficient, and graphite precipitates in the form of flakes to form gray iron structure.
Problems with pouring speed and filling. When the pouring speed is fast, the lower molten iron is greatly impacted and disturbed when the molten iron fills the cavity, causing uneven distribution of the spheroidizing agent and easy inclusion of gas, affecting the spheroidization effect; at the same time, fast pouring may cause the lower graphitization degree to decrease due to fast heat dissipation and fast solidification, forming gray iron. Slow pouring speed can easily cause the molten iron to oxidize and inhale seriously during the pouring process, resulting in large loss of spheroidizing elements and affecting the quality of spheroidization in the lower part.
Elements such as carbon and silicon in the molten iron segregate during the solidification process. The carbon and silicon content in the lower part is relatively low, and the graphitization ability is weakened, which promotes the formation of gray iron structure; the carbon and silicon content in the upper part is sufficient, which is conducive to the formation of ductile iron structure.
The molten iron itself has component segregation. The content of anti-spheroidizing elements in the upper molten iron is low, and the spheroidization is normal. The bottom molten iron may contain more anti-spheroidizing elements, which will significantly consume magnesium or hinder graphite spheroidization. Leading to the production of gray iron.